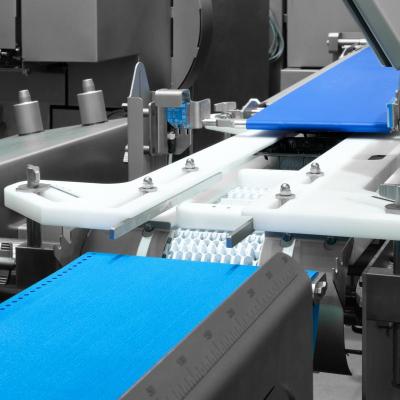
In an ideal world, every bit of dust, debris or residue from the manufacturing process will be reduced or completely eliminated from the final quality and packaging controls. It’s like receiving your favorite package of cookies with each product perfectly shaped, sized and facing the proper direction, in pristine packaging.
As cookies movie along a conveyer belt and into a vibratory bowl feeder, the resulting rotational and centrifugal forces cause the delicious sweets to bump along the sides of the feeder panels and into each other; thus a crumb trail begins to appear. The once perfectly-shaped cookie becomes asymmetrical, and picks up debris along its path.
Photosensitive sensors can be deployed along the supply line to detect residue and ensure material integrity. Some sensors are equipped with infrared high-performance LEDs, allowing for cleaning cycles, as sanitation and consistency of products are key factors in the automation of industrial food processing. While the growing demand for various shapes and sizes of food products continues to increase the diversity of manufacturer selections, reducing the crumb trail left behind by part-feeding systems through light sensors has the potential not only to minimize cross-contamination, but to get one step closer to that consistently-perfect cookie!
Find out more about part-feeding solutions that avoid the crumb trail.
Sources:
https://www.di-soric.com/static/pages/2019/09/mz_en.html
https://www.autodev.com/vibratory-parts-feeding-tips/parts-feeding-tip-eliminating-dead-spots
https://www.hoosierfeedercompany.com/food-and-beverage